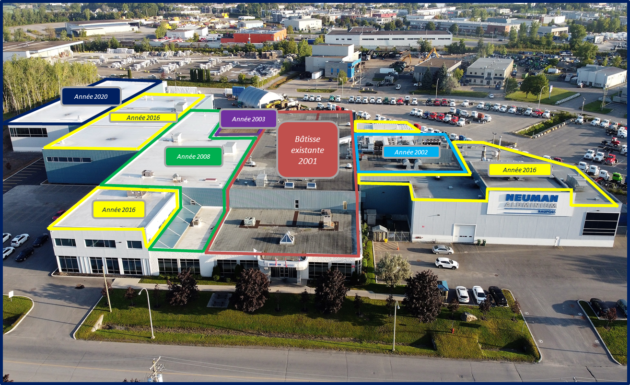
Raufoss Technology’s manufacturing facilities showing their expansions and updates over the years (Credit: Raufoss Technology)
Raufoss Technology announced an $18M investment into its manufacturing operations at the beginning of May, mentioning plans to increase its robotics, automation and investments to increase and replace plant lines.
Canadian Manufacturing sat down with the CEO of Raufoss to ask about the company’s plans and challenges moving forward.
Q: This new announcement of $18M earmarked for new machinery is the latest in a series of investments being made by manufacturers involved in the EV manufacturing supply chain. How has this landscape changed over the last year?
Jean Meredith: There’s an imperative need now to set up the supply chain regardless of engine type. Carmakers need to reduce weight when it’s an EV, and we’re seeing more business now from carmakers with changing needs. We’re seeing business and requests for suspension components from Chinese OEMs that we had no idea existed even three years ago.
Q: How do you plan to spend this investment specifically?
JM: $3M will go towards improving plant lines. As a business we’ve grown by 300% over the last few years, and we’ve added and replaced lines. 80% of our current manufacturing operations are net-new in recent years.
Q: We’ve seen big investments announced in Ontario recently from automakers, I’m wondering how this affects a business based in Montreal, or does it have an adverse effect on the manufacturing supply chain the Quebec region?
JM: Our high level strategy is to be the most green supplier for components. We know we have clean electricity here in Quebec so we’re focused on optimizing the plant, improving our robotics operations and developing our staff.
Q: We’ve seen some manufacturers experience challenges with regards to labour and talent retention, how has the labour landscape effected Raufoss?
JM: The last two or three years have been challenging. We’ve hired 130 people over the last three years and it’s particularly challenging because we’re looking for highly skilled employees, this isn’t manual work anymore. We feel like we’ve hit a wall, but we’re trying to use the TFW program to bring more people in on contracts. Luckily, we are 100% staffed now.
Q: Is there anything you’d like to see changed that would make talent retention easier?
JM: We feel like the process could be quicker. When you have to bring someone in from outside Canada, it takes time. Currently, it takes around 12-18 months to bring them in, and as you know, that requires you to anticipate hiring challenges over a year in advance of when you’ll require the staff.
Q: When it comes to talent acquisition, are there any particular strategies that have helped Raufoss become more successful?
JM: There’s so much competition for talent from other industries, we’ve had to develop them through the college system. Raufoss has a program through a college that helps us find employees. They’re extremely well-qualified and they come right out of the college ready to contribute to the workforce.
Q: Where do you see the EV transition going from here, are we on target to develop the country’s EV manufacturing supply chain in your opinion?
JM: It needs to be a lot faster, but I think the market will actually slow down. We’re not at the pace we were hearing about a year or two ago. OEM’s are realizing that they can’t go at that speed, there’s a lot of questioning right now. The government tariffs being discussed right now would just be a patch to buy time, and I don’t see that as a long-term solution. China is so fast in developing EVs and its related technologies that we have to consider if countries like ours can even be fully electric.
Q: Finally, what do you want people to know about Raufoss Technology and what it’s trying to do in the marketplace?
JM: We’re trying to be experts in light-weighting. We have light-weighting solutions for OEMs and we’re involved in assembly and ball joint manufacturing to help reduce the weights of vehicles regardless of the type of engine.
Q: Thank you for your time!